Flow Synthesis
The history of organic synthesis began in the late 19th century, and examples of batch reactions in flasks have been reported since then. Continuous production systems for mass production, such as pipelines, have been used for a long time. And it was in the late 20th century that the micro flow reactions used in general organic synthesis started to attract attention. Flow reactions feature (1) high-speed mixing, (2) high heat exchange rate, and (3) accurate control of residence time, thereby allowing reactions under conditions where batch reactions cannot realized. The applicability of these reactors is increasing; for example, they can be used for a gas-liquid reaction, which is expected to increase contact surface area, and in column flow reactors that use highly active solid phase catalysts.
More Information
What is flow synthesis?
Useful molecules such as pharmaceuticals that we use today are mainly synthesized by the "batch method" in which the product is purified after the reaction is carried out using a large reaction vessel. While the batch method can synthesize compounds with complex structures in multiple steps, there are problems that it is necessary to purify synthetic intermediates at each step and that a large amount of waste is discharged after the reaction (Fig. 1 left). In addition, when the reaction is carried out on a large scale, problems of heat transfer and stirring efficiency also occur. On the other hand, the "flow method" is attracting attention as a method that can solve these problems (Fig. 1 right). The flow method has been known for a long time, but it has the advantage that the target compound can be obtained without isolating and purifying the intermediate by flowing the raw materials step by step through the column. Furthermore, the advantages of the flow method are high reaction efficiency because the reaction is carried out using a small reaction vessel (especially when using a microreactor), and stable supply is possible because the reaction conditions can be precisely controlled by a machine.
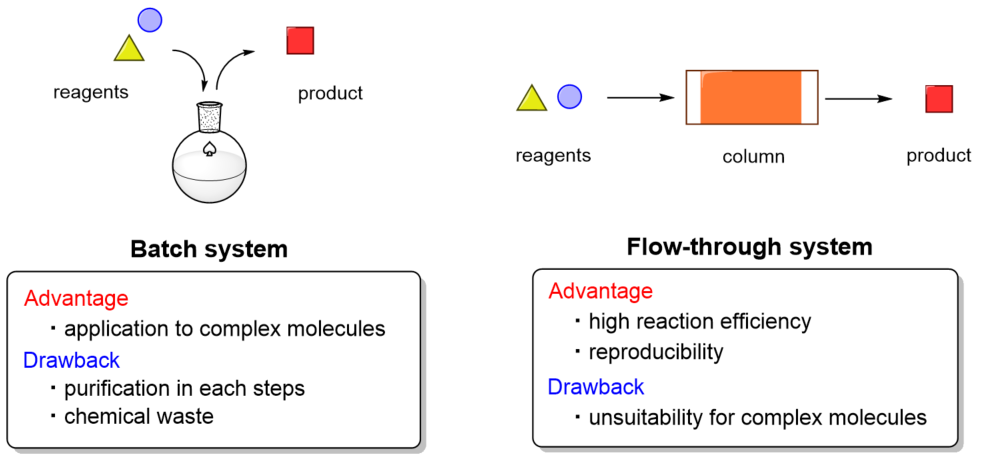
Classification of catalytic reactions by the flow method
The reactions by the flow method can be roughly classified into the following four types (Fig. 2).
Non-catalytic type (Type I) |
Reactants A and B are poured and reacted in a column. At this time, unreacted substrate and by-products come out from the column at the same time as the product, so purification operation after the reaction is required. |
---|---|
Supported reagent type (Type II) |
B is immobilized on a column and A is allowed to flow to react. Reactor B immobilized on the column is consumed as time progresses, so a new column is required. |
Homogeneous catalyst type (Type III) |
A and B and the catalyst are allowed to flow together to react. Although the reaction proceeds efficiently due to catalytic action, it is necessary to remove the catalyst from the product. |
Heterogeneous catalyst type (Type IV) |
A and B are flowed through a column on which a catalyst is immobilized to react. At the same time as the reaction proceeds smoothly, it is possible to prevent catalyst contamination unlike Type III. |
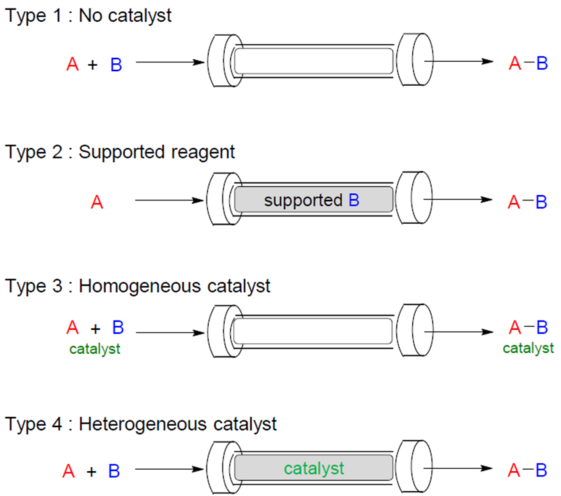
Reference
"Multistep Continuous Flow Synthesis of (R)- and (S)-Rolipram Using Heterogeneous Catalysts"
Tsubogo, T., Oyamada, H., and Kobayashi, S.:Nature, 520, 329 (2015). DOI:10.1038/
For research use or further manufacturing use only. Not for use in diagnostic procedures.
Product content may differ from the actual image due to minor specification changes etc.
If the revision of product standards and packaging standards has been made, there is a case where the actual product specifications and images are different.