Let's learn RAFT polymerization remotely!
Types of RAFT agents
RAFT polymerization is a reversible addition-fragmentation chain transfer living radical polymerization method, and it is effective in the synthesis of polymers with a narrow molecular weight distribution. In order to conduct RAFT polymerization efficiently, it is necessary to select a suitable RAFT agent considering the reactivity of the monomer species to be used in polymerization. Please see the article here for the reaction schemes of RAFT polymerization.
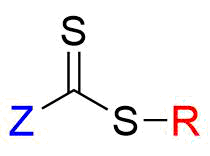
Fig.1 Basic structure of RAFT agent
The basic skeleton of the RAFT agent has a thiocarbonylthio group (S=C-S) that undergoes radical addition and fragmentation relatively easily (Figure 1). In RAFT polymerization, the radical formed from the initiator such as an azo polymerization initiator becomes attached to the monomer to form an oligomer radical, which then attaches to the C=S double bond of the RAFT agent. The intermediate radical formed at this time becomes rapidly fragmented to produce R•, and R• reacts with the monomer, thereby resuming and continuing the polymerization. Therefore, groups that have a substituent group such as a nitrile group, aromatic ring, and carbonyl group close to the carbon, which are likely to stabilize the radical, are used for the R part. In addition, substituent group Z has a large effect on the stability of the intermediate radical, and the rates of radical addition and fragmentation depend largely on the structure of Z. Table 1 shows the types of RAFT agents, classified by the difference in the substituent group Z.
Table 1 Classification of RAFT agents (It was a table in Japanese text, Needs correction)
How to select the RAFT agent
In general, RAFT polymerization is executed with a reagent concentration ratio of [monomer]:[RAFT agent]:[initiator] = 15 to 300:1:0.3 to 0.01, room temperature to 140°C, and normal pressure to 5 kbar, under heating or light irradiation with an azo compound being used as the initiator. There is no simple RAFT agent that can control all monomers, and we have to select an appropriate RAFT agent based on the individual monomer, polymerization conditions, etc. Figure 2 shows the types of monomers that are effective for substituent groups Z and R of the RAFT agent (Figure 1).
Figure 2 Compatibility between substituent groups Z and R of the RAFT agent and monomer. (The substituent group Z is listed in descending order of the chain transfer constant. The substituent group R is listed in the descending order of fragmentation rate. Dotted lines indicate partial controls.)
Fig.2 Monomer compatibility with Substituents Z and R of RAFT agents
(Substituent Z is in descending order of chain transfer constant.
Substituent R is in order of fastest cleavage.
The dashed line represents partial control.)
Compatibility between RAFT agents and monomers
(1) to (7) of Table 2 show the compatibility tables between general monomers and RAFT agents. We can see that trithiocarbonates in (1) to (5) and dithioester in (6) are effective for polymerization of conjugated monomers such as MMA. The choice of RAFT agent is also influenced by the polarity of the propagating radical that attacks. In the polymerization of vinyl acetate, in which N-vinyl-pyrrolidone and N-vinylcarbazole, etc., provide nucleophilic radicals, agents such as dithiocarbamates in (7) and dithiocarbonates (Table 1 (D)) are used. The Q value by Alfrey-Price can be used as a reference for whether the monomer to be used is conjugated or non-conjugated.
While dithiobenzoate (Table 1 (A)) is an excellent RAFT agent, it should be noted that it decomposes in reaction with acids. Therefore, this RAFT agent cannot be used for polymerization that uses acid, such as emulsified polymerization and suspension polymerization that use acid as a stabilizing agent, or three-dimensional structure control polymerization that uses Lewis acid. Trithiocarbonate (Table 1 (B)), which is relatively less likely to be hydrolyzed, is used instead.
Table 2 Matching table of RAFT agents and monomer species
Examples of polymerization
As specific examples of living radical polymerization with RAFT, Table 3 and Figure 3 show the results of bulk polymerization of n-butyl acrylate and the SEC curve obtained from block copolymerization of the same monomer. The RAFT agent shown in Table 2 (1) and initiator V-60 were used, with the reaction temperature 70°C.
Table 3 Molecular weight, molecular weight distribution, conversion rate of homopolymer obtained by bulk polymerization of butyl n-acrylate by RAFT polymerization
(RAFT agent: Table 2 (1), initiator: V-60, reaction temperature: 70°C)
Fig.3 Poly (n-butyl acrylate) homopolymer obtained from RAFT Agent 1 (Table 2)
(Mn=25,900 g/mol, Mw/Mn=1.09) and n-butyl acrylate derived from the homopolymer- SEC curve 5 of n-butyl acrylate block copolymer (Mn=150,100 g/mol, Mw/Mn=1.11))
Table 3 clearly shows that the molecular weight of the polymer increases almost linearly with the calculation as the time of polymerization passes, and that the molecular weight distribution (Mw/Mn) is also small. In addition, the SEC curve shows that the addition of the monomer to the reaction system causes the polymerization to start again and increases the molecular weight of the polymer. Synthesis of block copolymers with various properties becomes possible by changing the type of monomer here.
Examples of specific combinations of RAFT agents, monomers and polymerization conditions have been summarized by Moad et al. If you want to know more detailed examples and conditions of polymerization, please be sure to refer to them.